Cast vs Forged and 3D Billet Pistons
The picture to the right shows a precision die-cast piston (left) and a precision forged piston.
There are three ways that we produce piston blanks prior to machining.
Die casting-
This process requires the melting of a special high silicon alloy in an electric furnace with extremely closely controlled temperature. The molten alloy is then poured into a multi-piece die producing a very accurately shaped piston casting. The casting die is manufactured so that when the metal has solidified the various pieces of the die can be extracted one by one. This means that undercuts and reliefs can be produced in the casting to reduce the piston weight. The cost of a die-cast piston is considerably less that that of forgings but their use is limited to road going vehicles, vintage car clubs and motorcycle clubs. Having said that, we have produced Mini pistons for both road and race applications using this process with excellent results.
Forging-
The production of piston forgings is more complex than the casting process and some 80% of our pistons are produced in this way. The main material used is RR58 (2618A). Two other alloys are used, one is a high silicon alloy and the other is a Metal Matrix Composite alloy. The specification of these alloys must remain confidential at the moment.
The forging process requires material to be bought in at closely controlled diameters, this is then cut to billet size and all cut faces machined to a smooth finish. The billet is pre-heated in an air-circulating furnace to a temperature quite close to the operating temperature of the piston crown when the engine is operating at full power. This temperature is critical and cannot be disclosed. This together with tightly controlled speed of the forging process gives a dense and very fine grain structure to the forging. Microstructure analysis of our forgings and that of other manufacturers will highlight this difference. This fine grain structure gives our forgings higher strength and fatigue life. After forging, any excess material is removed and the forgings are then heat-treated followed by wet blast cleaning.
Three Dimensional Machining.
The best way for a small batch of pistons to be made that have to have no compromise or, for prototyping to finalise a design before a forging tool is manufactured is 3D machining. The piston is designed using our state of the art 3D modelling software and each piston is individually machined from a solid billet. This takes approximately ninety minutes depending on the complexity of the final internal shape. After this process it is then passed on to the workshop for wet blast cleaning, and all of the external machining. Though expensive it is sometimes the only way a customer can get exactly what they want for a small production batch. To the untrained eye it is very difficult to tell a 3D machined billet piston from a forged piston.
For more information view our technology section. |
|
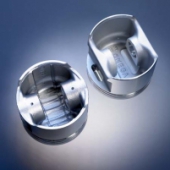 |